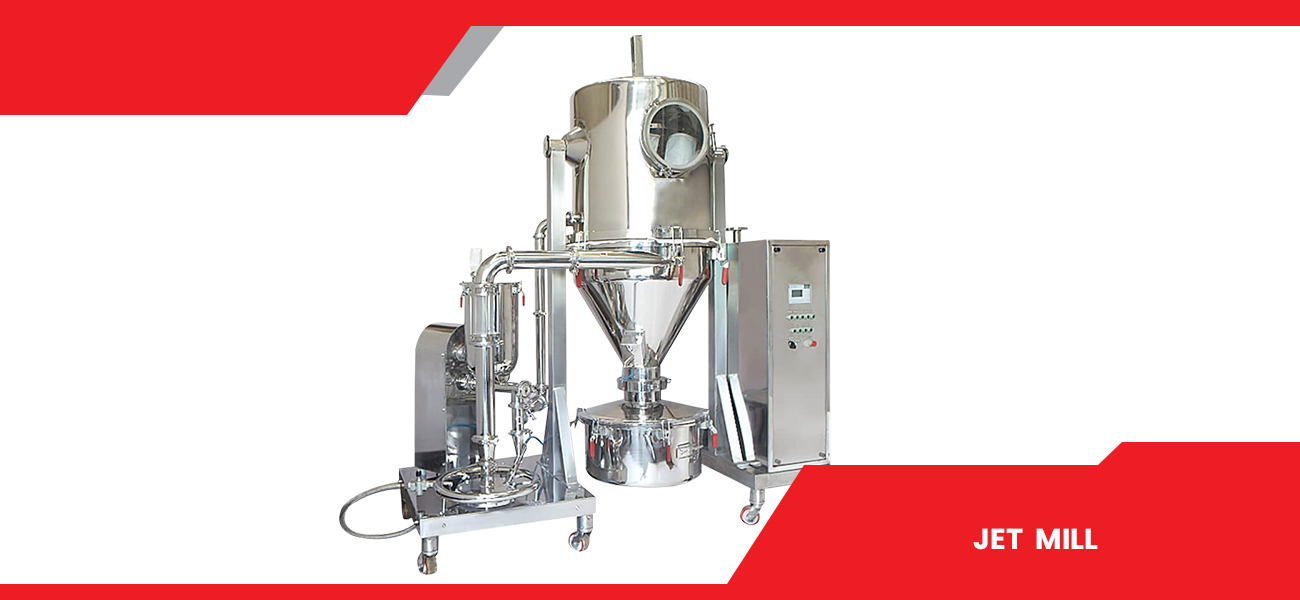
- Home
- Jet Mill
Jet Mill
JET MILL WORKING PRINCIPLE:
“ PHARMA FAB INDUSTRIES “ How dose a jet mill work? This article aims to describe the working principle of a jet mill. A jet mill, also called fluid energy mill, is used for solid material micronization.
Micronization is a term used to describe size reduction where the resulting particle-size distribution is less than 10 microns. Jet mills are used for micronizing of solids of chemicals, pharmaceuticals, pigments, minerals and others like heat sensitive, corrosive and abrasive materials.
In many cases, the micronization process is often considered as a black box that produces fine powder and coarse particles enter. Jet mills operate in compressed air, gas or high pressure superheated steam. Jet mills have no moving parts, thereby eliminating contamination due to contact with external grinding media. It is also an ideal process to grind heat-sensitive and waxy material because no attritional heat is generated.
Jet mill works on fluid energy. Consider a pancake spiral jet mill as an example. Micronizing and classification take place in a shallow, cylindrical chamber. High pressure air or steam is injected in this chamber through the specially designed nozzles placed at regular distance, on the peripheral wall. The axis of each jet is tangential to the circumference of a smaller, imaginary, concentric circle.
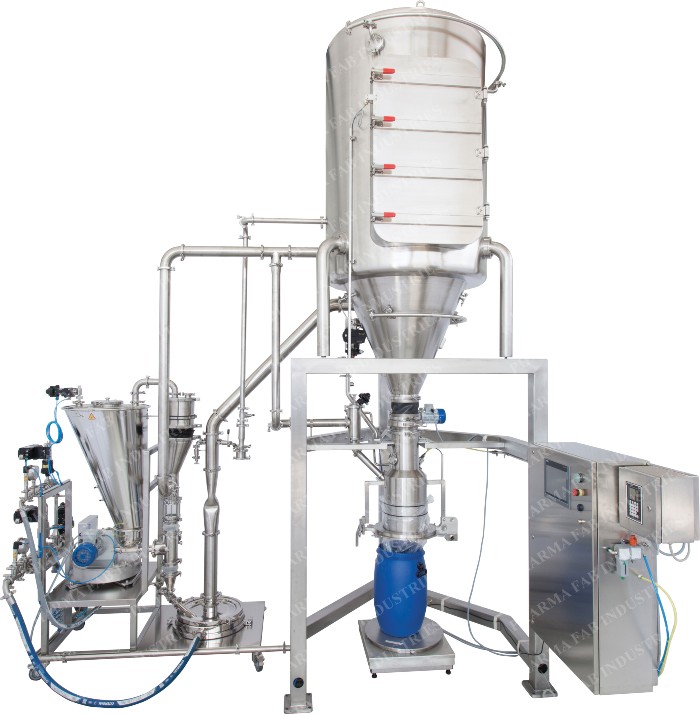
During operation, the material is fed into this vortex along an engineered tangent circle and accelerates. Strong velocity gradients near the jet cause the suspended particles of the material to collide with each other and reduce themselves by attrition and collision. Size reduction is the result of the high-velocity collisions between particles of the process material itself. No grinding media is involved. The jet fluid exits through an outlet at the center of the chamber either from top and draws the micronized the particles with it to the cyclone collection system. Heavier oversized particles are held in the grinding chamber by centrifugal force, until micronized to a desired size.
Feed particle size is critical, restricted by the size of the feed injector. For mills of 200-300 mm, the feed size can be a maximum of 1.5 mm. For smaller-size mills, the feed size is correspondingly finer.
There are several factors, both operational and physical, which affect the fineness of the end product, such as feed rate, nozzle size, nozzle pressure, nozzle angle, airflow rate, feed particle size, chamber diameter and width, and product outlet diameter. All of these variables can be adjusted during operation, but it is more likely that once operation has begun, only feed rate will be varied to meet the required particle-size distribution.
Actually the spiral jet milling process is not governed only by the jet mill itself. It is a process involving different machines and components which need to be properly integrated and controlled. These accessories include a source of fluid energy, a feeder, a cyclone separator, a dust collector etc.
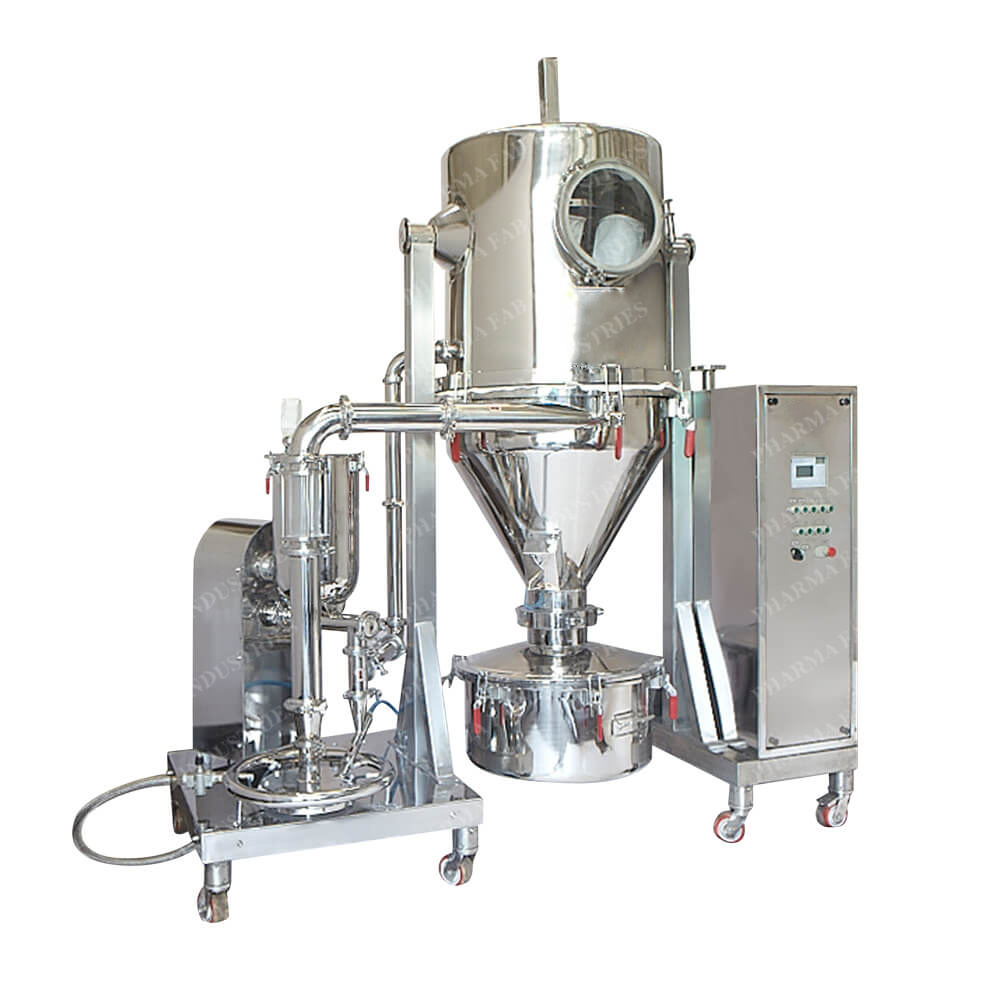
JET MILLING EXAMPLE :
The demand for pharmaceutical materials including finely ground active substances and excipients is growing. Inject able drugs and dry powder inhalants require particle-size distributions in the range of 2-20 microns with a steep distribution curve and a minimum of fine and over-sized particles. Jet milling is a highly effective technology for reducing particle size of inhalation and other drug products where the size of the particle is relevant to the effective delivery.
ADVANTAGES OF JET MILLS :
- No mechanical moving parts
- Easy components cleaning
- Very fine particle dimensions obtained
- Constant temperature and no heat generated
DISADVANTAGES OF JET MILLS :
- Relatively lower productivity
- Large equipment size with necessary accessories
- High process gas flow
APPLICATION :
- Agrochemicals : Deltamethrin, Carbendazim, Carbaryl, Germicide, Herbicide, Fungicide etc.
- Chemicals : Adipic acid, Barium titanate, Calcium chloride, Chromium oxide, Catalyst etc.
- Ceramics : Aluminium hydrate, Silicon carbide, Ferrite, Glass, Zirconium oxide etc.
- Minerals : Bauxite, Gypsum, Graphite, Mica, Talc, Tentalum ore etc.
- Paints : Carbon black, Fluorescent pigment, Titanium dioxide etc.
- Pharmaceuticals : Amino Acid, Antibiotics, Aspirin, Guanylate, Furosemide, Penicillin, Vitamin Compound etc.
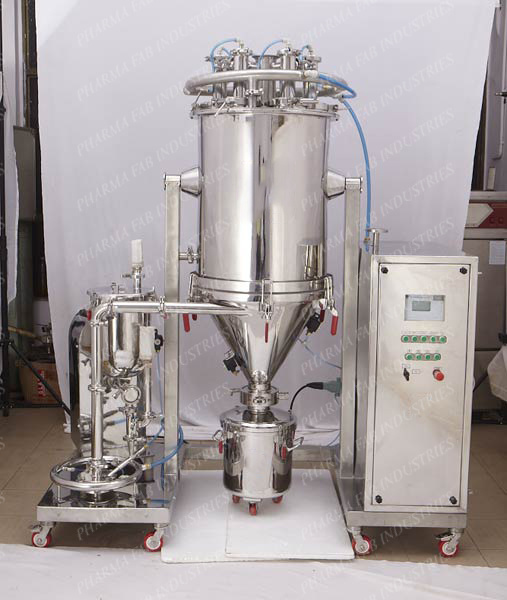